Basic Knowledge about Ultrasonic Testing
Background
Non-visible and mostly hidden defects in almost all components can be detected non-destructively by means of ultrasound. Ultrasonic testing is particularly important for safety-relevant components. In addition, mere measurements are possible as well; the best known of these is the wall thickness measurement.
The main applications are:
- On-site inspection of welded joints
- Defect inspection and quality control of castings
- Automatic testing of mass products with simple geometries such as semi-finished products (round material, billets, profiles, sheets and tubes) made of steel, non-ferrous metals and plastics
- Wall thickness measurements on pipelines, vessels and chemical plants. Wall thickness measurement by means of ultrasound is useful wherever the measuring point is only accessible from one side and a caliper gauge cannot be used.
Advantages of Ultrasonic Testing
- Detection of surface and internal defects (hidden from the surface)
- All materials with good sound conductivity can be tested (up to 10 m if necessary)
- The process can be automated
- No special radiation protection regulations need to be followed
- Reliable detection of planar flaws (laminations, cracks, lack of fusion, …)
Principle
The definition of ultrasound covers sound components with a frequency above the human hearing threshold, i.e. more than 20,000 Hertz (= 20 kHz). The main frequency range for ultrasonic testing is 0.5 MHz to 10 MHz, which is well above the hearing threshold. For special applications the examination frequency can also take values above 10 MHz or below 0.5 MHz.
Testing in Detail
When an ultrasonic wave hits an interface (between medium 1 and medium 2) one part is reflected and another part is transmitted. Their ratio depends on the differences between the two adjacent media (e.g. with respect to sound velocity and density). At the transition point from steel to air, the difference is very large and results in a reflected ultrasonic wave of almost 100 % .
Defects in a component usually are made up of air inclusions (blowholes, pores, cracks, …). Therefore, the ultrasound wave is well reflected and, under favourable conditions, returns to the probe. To ensure that the air gap between the probe and the component does not interfere, a usually liquid coupling medium (water, oil, gel, etc.) is used. For automated testing, the entire component including probes often is immersed in water.
The sound velocity is a material constant and amounts to 330 m/s in air (at 0 °C; 344 m/s at 20 °C) and 5920 m/s in steel. If the sound velocity of the material to be tested is known, the depth position of the defect can be determined quite precisely from the transit time of the ultrasound. If the transit time to the opposite back wall is evaluated, the ultrasonic method can also be used for wall thickness measurement. Here a resolution down to the micrometer range can be achieved. The wall thickness gauges can be simplified and scaled down so that only the wall thickness value is displayed.
Less favorable is the determination of the defect size. Reliable evaluation methods unfortunately do not exist. Therefore, the amplitude of the reflected ultrasonic signal is usually compared with the reflected amplitudes of reference defects (circular disk-shaped reflectors, cylindrical reflectors, …). However, the prerequisite is always that the defect (and also the reference defect) is hit favorably by the sound.
The dimensions of those defects still detectable are in the ultrasonic wavelength range. Under favorable conditions, this range can start at a few tenths of a millimeter. In less favorable cases, defects can only be detected from millimeter sizes upwards.
Angle probes are used not only, but mainly, for weld seam inspection because coupling on the usually uneven welding bead with vertical probes does not allow reliable testing. The so-called angle of incidence depends on the defects to be detected (here, as well, the defects need to be insonificated from a advantageous direction).
Acoustic Material Properties
Information on the acoustic material properties of various materials, such as longitudinal and transverse sound velocity, density and acoustic impedance can be found in the following tables.
The values for sound velocity, density and acoustic impedance listed in the tables are valid for room temperature (20 °C to 23 °C). Variations due to material composition, crystal orientation, porosity and temperature are possible.
Source: “Ultraschallprüfung (translates to ‘Ultrasonic Testing’)” (Deutsch, Platte, Vogt), Springer Verlag 1997
Metals
Metals | Sound Velocity (longitudinal wave) cl [m/s] |
Sound Velocity (transverse wave) cl [m/s] |
Density [103 kg/m3] |
Acoustic Impedance [106 kg/m2s] |
Aluminium | 6200 – 6360 | 3100 – 3130 | 2.7 | 16.7 – 17.2 |
Beryllium | 12720 – 12890 | 8330 – 8880 | 1.82 – 1.87 | 23.2 – 24.1 |
Brass (Ms58) | 3830 – 4250 | 2050 – 2200 | 8.1 | 31.0 – 34.4 |
Cadmium | 2665 – 3300 | 1500 – 1810 | 8.6 – 8.7 | 22.9 – 28.5 |
Carbide | 6800 – 7300 | 4000 – 4700 | 11.0 – 15.0 | 74.8 – 109.5 |
Cast Iron | 3500 – 5800 | 2200 – 3200 | 6.9 –7.3 | 24.2 – 42.3 |
Constantan | 5240 | 2640 | 8.8 | 46.1 |
Copper | 3666 – 4760 | 2260 – 2320 | 8.9 | 32.6 – 42.4 |
Gold | 3240 | 1200 | 19.7 | 63.8 |
Grey Cast Iron | 3500 – 5600 | 2200 – 3200 | 7.2 | 25.2 – 40.3 |
Iron | 5950 | 3220 – 3240 | 7.9 | 47.0 |
Lead | 2050 – 2400 | 700 – 710 | 11.3 – 11.7 | 23.2 – 28.1 |
Magnesium | 4602 – 5900 | 3050 – 3280 | 1.70 – 1.75 | 7.8 – 10.3 |
Molybdenum | 6250 – 6650 | 3350 – 3510 | 10.1 – 10.2 | 63.1 – 67.8 |
Nickel | 4973 – 6040 | 2960 – 3219 | 8.8 – 8.9 | 43.8 – 53.8 |
Platinum | 3960 – 4080 | 1670 – 1730 | 21.4 | 84.7 – 87.3 |
Silver | 3600 – 3790 | 1590 – 1690 | 10.4 | 37.4 – 39.4 |
Tin | 3210 – 3320 | 1530 – 1670 | 7.3 | 23.4 – 24.2 |
Titanium | 5823 – 6260 | 2920 – 3215 | 4.5 | 26.2 – 28.2 |
Zinc | 3890 – 4210 | 2290 – 2440 | 7.1 | 27.6 – 29.9 |
Non-Metals
Non-metals | Sound Velocity (longitudinal wave) cl [m/s] |
Sound Velocity (transverse wave) cl [m/s] |
Density [103 kg/m3] |
Acoustic Impedance [106 kg/m2s] |
Aluminium Oxide | 9000 – 11000 | 5500 – 6500 | 3.6 – 3.95 | 32.4 – 43.5 |
Epoxy resin | 2400 – 2900 | 1100 | 1.1 – 1.25 | 2.64 – 3.63 |
Glass (Quartz glass) | 5570 – 5930 | 3415 – 3750 | 2.6 | 14.5 – 15.4 |
Glass (Window glass) | 5770 | 3430 | 2.51 | 14.5 |
Graphite, pressed | 1600 – 2500 | 1200 – 1500 | 1.7 – 2.3 | 2.72 – 5.8 |
Ice (H2O at -4 °C) |
3232 – 3980 | 1990 | 0.9 | 2.9 – 3.6 |
PA (Polyamide) | 1800 – 2600 | 1100 – 1200 | 1.1 – 1.2 | 1.98 – 3.12 |
PE (Polyethylene) | 1950 – 2000 | 540 | 0.9 | 1.76 – 1.80 |
PMMA (Plexiglass®) | 2670 – 2760 | 1120 – 1430 | 1.18 | 3.2 – 3.3 |
Polystyrene | 2337 – 2350 | 1020 – 1150 | 1.05 – 1.06 | 2.45 – 2.49 |
Porcelain | 5600 – 6200 | 3500 – 3700 | 2.4 – 2.5 | 13.4 – 15.5 |
PTFE (Teflon®) | 1350 | 550 | 2.2 | 2.97 |
PVDF (Polyvinylidene-fluoride) | 2200 | 775 | 1.78 | 3.9 |
PVC (Polyvinyl chloride) | 2180 – 2260 | 948 | 1.38 – 1.40 | 3.0 – 3.2 |
Quartz Crystal | 5760 | 3840 | 2.65 | 15.2 |
Rubber, hard | 1570 – 2300 | – | 1.2 | 1.88 – 2.76 |
Rubber, soft | 1480 – 1550 | – | 0.90 – 0.95 | 1.33 – 1.47 |
Steel
Steel | Sound Velocity (longitudinal wave) cl [m/s] |
Sound Velocity (transverse wave) cl [m/s] |
Density [103 kg/m3] |
Acoustic Impedance [106 kg/m2s] |
Mild steel, unalloyed up to 0.2 % C, e. g. St 52-3 acc. to. DIN 54120 | ||||
–annealed –annealed to 0.5 % C |
5890 – 5950 5940 – 5960 |
3240 – 3270 3230 – 3245 |
7.85 7.8 – 7.85 |
46.2 – 46.7 46.3 – 46.8 |
Mild steel, alloyed (0,35 % C, 0,6 % Mn, 1 % Cr, 0,2 % Mo) | ||||
–annealed –remunerated –hardened |
5950 5930 5900 |
3260 3240 3230 |
7.84 7.84 7.84 |
46.6 46.5 46.3 |
Mild steel, alloyed (0,3 % C, 0,4 % Mn, 2 % Cr, 2 % Ni, 0,2 % Mo | ||||
–annealed –remunerated –hardened |
5930 5870 – 5880 5890 |
3220 3210 3210 |
7.85 7.85 7.85 |
46.6 46.1 – 46.2 46.2 |
Ball bearing steel (1 % C, 1,5 % Cr) | 5990 | 3270 | 7.8 | 46.7 |
Stainless steel, austenitic | ||||
–(X 10 Cr Ni 18 8) annealed’ –(X 10 Cr Ni Nb 18 9) –(X 12 Cr Ni 18 8) |
5530 5790 5660 |
2983 3100 3120 |
7.-9 7.8 – 7.9 7.8 |
43.7 45.2 – 45.7 44.1 |
Stainless steel, ferritic (0,15 % C, 17 % Cr) | ||||
–annealed | 6010 | 3360 | 7.7 – 7.9 | 46.3 – 47.5 |
High Speed Steel (0,9 % C, 4 % Cr, 2,5 % Mo, 2,5 % V, 3 % W) | ||||
–annealed –hardened |
6060 5880 |
3850 3190 |
– | – |
Tool Steel (1 % C) | ||||
–annealed –hardened |
5940 – 5960 5854 |
3220 – 3245 3150 |
7.8 – 7.84 7.84 |
46.3 – 46.7 45.9 |
Tool Steel (2 % C, 12 % Cr, 0,6 % W) | ||||
–annealed –hardened |
6140 6010 |
3310 3220 |
7,75 – 7,8 7.75 |
47.6 – 47.9 46.6 |
Further Information
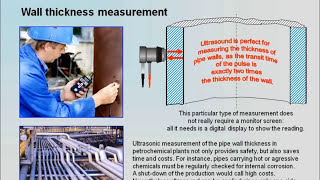
Further, comprehensive information on ultrasonic testing can be found in our knowledge floater video “Ultrasonic Material Testing”.